Imagine a virtual replica of a physical object, constantly learning and evolving, mirroring its real-world counterpart in real-time. This isn’t science fiction; it’s the fascinating world of digital twins. Digital transformation has maximised the efficiency of various technologies, while digital twins, beyond their contemporary benefits, provide substantial environmental advantages. These virtual counterparts have the potential to unlock an additional $1.3 trillion in economic value and reduce CO2 emissions by 7.5 Gt by 2030.
But where did this concept originate, and how is it revolutionising various industries, let’s delve deeper into it:
The Birth of Digital Twins
The concept of digital twins can be traced back to the early days of aerospace engineering. In the 1960s, NASA’s Apollo program utilised a form of digital twinning to create simulations of spacecraft for mission planning and risk assessment. However, the term “digital twin” wasn’t formally coined until 2002 by Michael Grieves, a professor at the University of Michigan. Since then, the concept has gained significant traction across various sectors.
Varieties of digital twin in Battery Manufacturing:
Depending on the application, there are mainly three types of digital twins:
- Digital machine twin: Encompassing all production-relevant machinery within the factory.
- Digital product twin: Integrating information, quality data, and other attributes regarding raw materials and all intermediary and final products, along with parameters from various processing operations.
- Digital building twin: Encompassing all components and necessary information for the construction and functioning of the factory building.
The digital twins of machines, products, or buildings are consolidated within the digital twin of battery cell manufacturing.
How Digital Twins Work
At its core, a digital twin is a virtual replica of a physical battery. Think of it as a software doppelganger constantly learning and mirroring its real-world counterpart. Sensors embedded within the battery feed data like temperature, voltage, current flow, and even user behaviour patterns to this digital twin. Using advanced analytics and machine learning algorithms, the digital twin processes this data to create a dynamic model. This model essentially becomes a digital reflection of the battery’s health and behaviour in real-time.
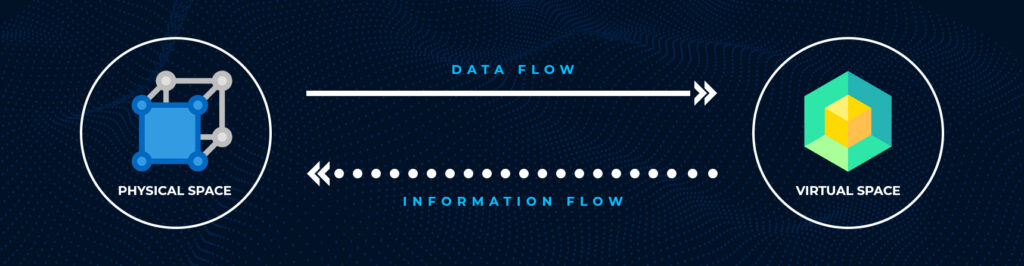
Why Digital Twins are a Game Changer for Batteries
The global digital twin market is expected to reach a staggering $90.7 billion by 2028, with a compound annual growth rate (CAGR) of 38.2%. A Deloitte report states that 78% of manufacturers are already using or plan to use digital twins in their operations. Here are some spectrums where the power of digital twins lies:
- Predictive Maintenance: By analysing data trends, digital twins can anticipate potential problems like cell degradation or thermal runaway before they occur. This allows for proactive maintenance, preventing costly downtime and extending battery life. A study by Gartner predicts that by 2022, at least half of industrial companies would utilise digital twins for predictive maintenance, highlighting its growing importance.
- Enhanced Battery Health: Digital twins can monitor factors like temperature and charging cycles, suggesting optimal charging strategies to maximise battery lifespan. This translates to fewer battery replacements and a reduced environmental footprint.
- Improved Safety: Real-time monitoring allows for early detection of safety concerns within the battery, preventing potential hazards like overheating or thermal runaway. This is crucial for ensuring the safe operation of batteries, especially in applications like electric vehicles.
- Reduced Development Costs: Digital twins can be used to virtually test different battery designs and configurations before physical prototypes are created. This reduces the need for expensive physical testing and experimentation, leading to faster development cycles and lower overall costs.
- Improved Design: By simulating various operating conditions and potential failure scenarios in a virtual environment, digital twins can help identify and address safety concerns early in the design phase. This leads to safer battery systems and minimises the risk of accidents.
- Enhanced Recycling and Resource Management: Digital twins can track the life cycle of a battery, including its degradation patterns and materials composition. This information can be used to optimise recycling processes, recover valuable materials, and minimise environmental impact at the end of a battery’s lifespan.
- Streamlined Supply Chain Management: Digital twins can be integrated with supply chain management systems to provide real-time data on battery performance and health across different stages of the battery life cycle. This allows for proactive maintenance and optimization of battery logistics, reducing downtime and ensuring efficient resource allocation.
- Improved Customer Experience: By leveraging data from digital twins, battery manufacturers can provide customers with personalised recommendations for battery care, maintenance, and charging strategies. This translates to a more informed and empowered user experience, leading to increased customer satisfaction and loyalty.
How does it affect research and development in Sodium-Ion battery technology?
Digital twins can revolutionise research and development (R&D) in sodium-ion battery technology by acting as a powerful virtual laboratory. This technology can help Sodium ion cell technology quickly catch up with Lithium Ion cells if the learnings can be digitised via a digital twin. A study by Accenture found that companies that embrace digital twins can achieve up to 30% improvement in operational efficiency. It is evident that companies with advanced digital capabilities experience revenue growth that is 2.5 times faster
Here’s how:
Accelerating Development:
- Virtual Testing: Forget expensive physical prototypes! Digital twins allow researchers to test different materials, electrolytes, and cell configurations virtually. This significantly speeds up the development process, leading to faster innovation cycles for sodium-ion batteries.
- Data-Driven Insights: Digital twins act as data sponges, collecting information on how various factors influence sodium-ion battery performance. Researchers can analyse this data to identify areas for improvement and optimise cell design for enhanced efficiency.
- Predictive Modelling: Digital twins can be used to create predictive models that simulate how sodium-ion batteries behave under different conditions. This allows researchers to anticipate potential problems like degradation mechanisms and tailor the cell design for optimal performance.
Enhancing Efficiency:
- Material Optimization: Digital twins help identify the most efficient material combinations for sodium-ion batteries. This can lead to batteries with higher energy density, faster charging times, and longer lifespans, all crucial for practical applications.
- Electrolyte Exploration: By simulating different electrolytes virtually, researchers can explore their impact on performance. This allows them to identify electrolytes that promote efficient ion transport and minimise internal resistance, leading to a more efficient battery.
- Charging Strategy Optimization: Data from digital twins can be used to develop optimal charging strategies for sodium-ion batteries. This minimises energy losses during charging and extends battery life while maximising performance.
- Understanding Degradation: Compared to lithium-ion batteries, sodium-ion batteries have unique degradation mechanisms. Digital twins can be used to study these mechanisms in detail, allowing researchers to develop strategies to mitigate them and improve battery longevity.
- Customization for Applications: Digital twins can be used to customise sodium-ion battery design for specific applications. By simulating different operating conditions, researchers can optimise battery performance for factors like power delivery, energy density, and lifespan based on the intended use case (e.g., electric vehicles vs. grid storage).
- Driving Sustainability: In the context of escalating climate change, the imperative to mitigate greenhouse gas emissions and minimise reliance on critical materials in battery cell production is paramount. Leveraging digital twin technology, manufacturers can harness data-driven optimization techniques to curtail the ecological footprint and resource consumption associated with battery manufacturing processes. By simulating various scenarios and monitoring real-time data, digital twins facilitate proactive decision-making to enhance efficiency and sustainability, aligning with the urgent need to address environmental concerns while meeting the growing demand for battery technologies.
- Operational Cost Reduction: Digital twins streamline production processes by offering real-time insights and simulations, cutting downtime and optimising resources, thereby reducing operational expenses. Predictive analytics anticipate demand fluctuations, minimising inventory costs, while data-driven decision-making guides equipment upgrades and resource allocation, driving down production costs while maintaining quality.
While Digital Twin technology is still in its early stages and ongoing research is being conducted, it is evident that the vision of a sustainable energy future is swiftly transitioning into a tangible reality. Everyday technologies like digital twins are offering a powerful ray of hope. A staggering 60% of organisations across major sectors are already leveraging this technology to drive their sustainability goals.
At Uneverse, we’ve always been committed to a greener path. That’s why we’re actively embracing digital twins for our sodium-ion cell technology. This innovation has the potential to make our batteries more efficient, durable, and cost-effective. Ultimately, it’s about contributing to a better world powered by clean and sustainable energy solutions. Are you with us?